LG Industries conçoit, fabrique et distribue ses propres produits. La production des parois et cabines de douche inclue la transformation du verre ainsi que le processus de « trempage ».
La transformation du verre flotté en paroi de douche est un processus de fabrication précis débutant par la création de verre float via flottage sur un bain d’étain. Le résultat est un verre plat et uniforme, essentiel pour une qualité optimale des parois. Notre float est de première qualité, garantissant une transparence et une clarté maximales.
Le verre est ensuite découpé aux dimensions souhaitées avec nos outils de précision, passant sur chacune de nos machines. Les bords sont du verre sont ensuite polis au diamant pour éliminer tout risque de coupure. Nous réalisons également un biseautage des bords et des angles afin de réduire les risques de casse lors de l’installation.
Ensuite, le verre subit une trempe thermique dans notre four de 60 mètres, le rendant jusqu’à cinq fois plus solide pour résister aux stress mécaniques ou thermiques des salles de bains.
Si nécessaire, un décor sérigraphié ou sablé est appliqué, tout comme un traitement de surface spécifique pour faciliter l’entretien. Notre traitement est l’anti traces Nano Care, sans PFOA, de fabrication allemande.
Les parois sont ensuite équipées de leurs profilés aluminium ou Inox, de fixations et de poignées en matériaux résistants et Design, avant de subir un contrôle qualité final rigoureux.
Ainsi produites, nos productions assurent sécurité, durabilité et une esthétique moderne pour les salles de bains.
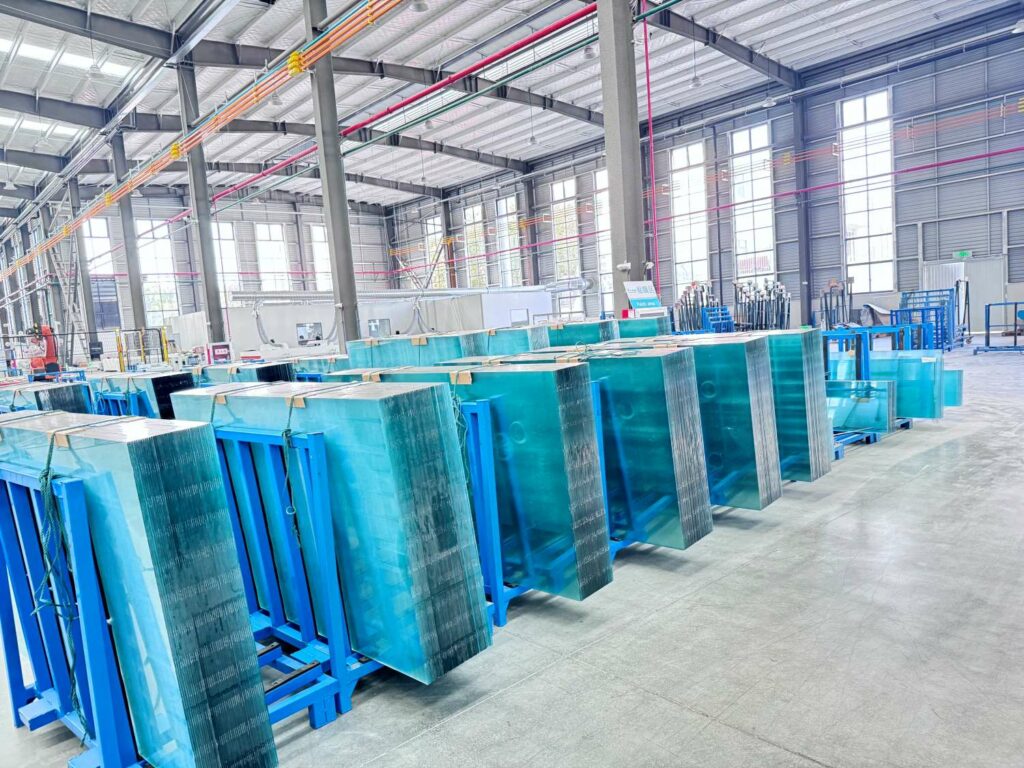
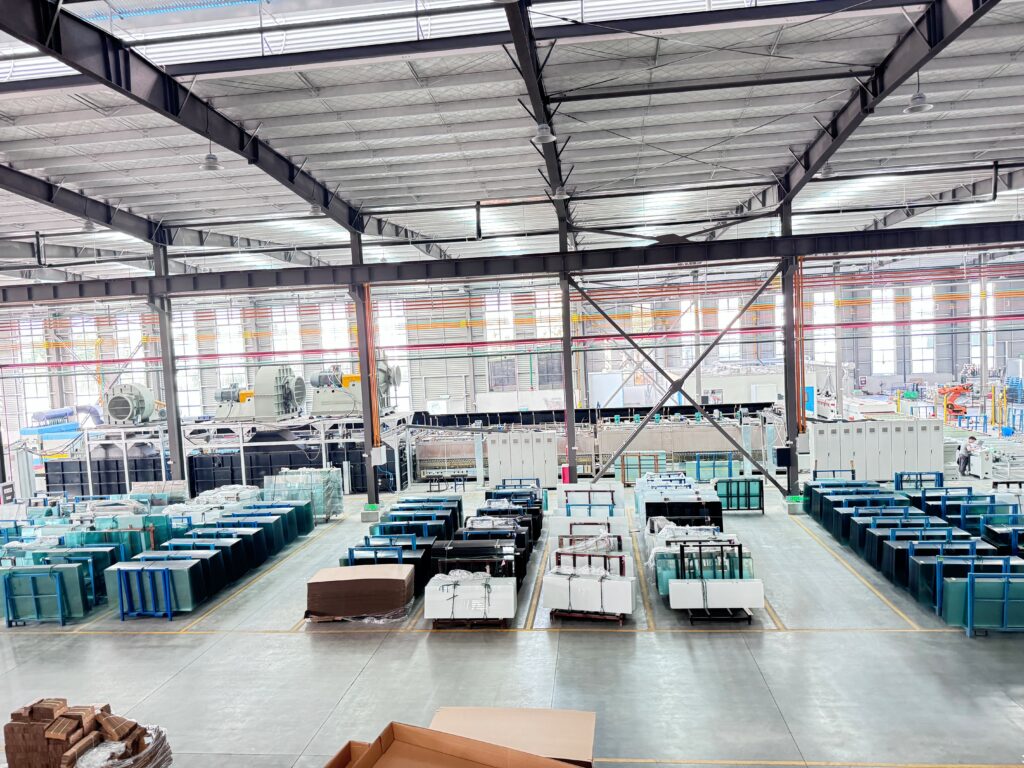
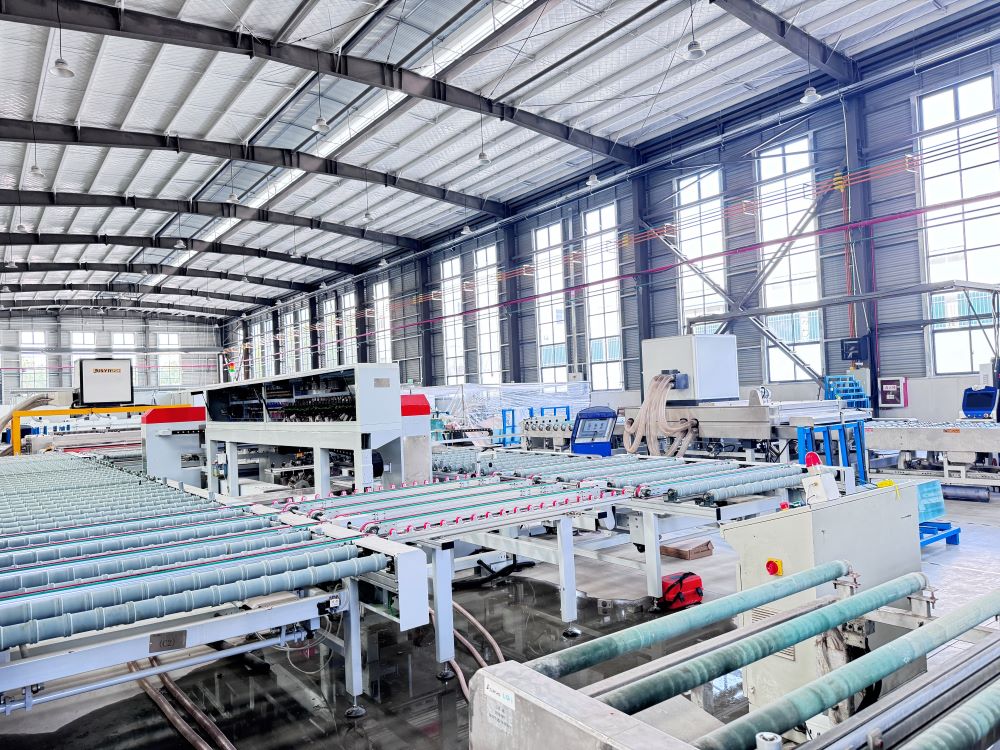
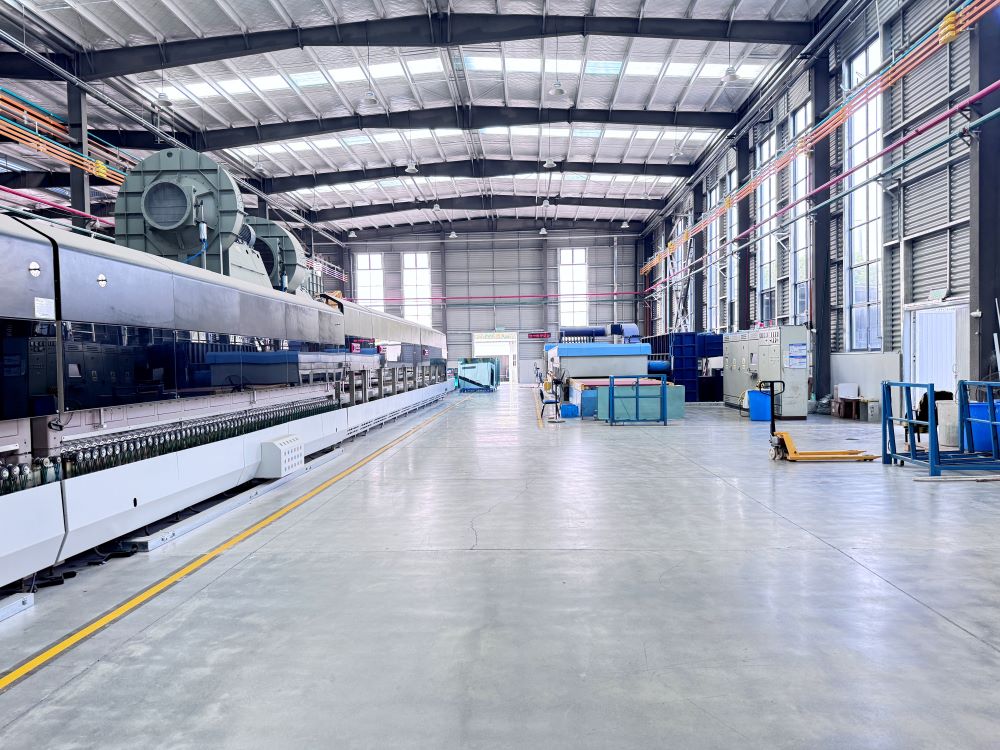
Le « float », ou verre plat, est travaillé sur notre outil de production. Mise à la taille, perçage, biseautage.
Des contrôles sont réalisés tout au long du process de production.
La qualité du float se décline selon son épaisseur, sa transparence et sa planéité. LG Industries utilise du float de première qualité.
Lorsqu’il s’agit des parois de douche, le choix du verre float est une étape cruciale, influencé par les exigences spécifiques de l’installation telles que la sécurité, l’esthétique et la durabilité. Les différentes épaisseurs de verre float jouent un rôle essentiel dans ces aspects : de 5 à 10mm d’épaisseur, il répond à une large palette de besoins : du standard 5mm à des produits positionnés Luxe en 10mm.
Dans notre four, le verre est monté à très haute température puis refroidi brusquement et séché. Ce procédé permet d’obtenir du verre de sécurité.
La norme européenne EN 12150, qui régit le verre trempé de sécurité, spécifie que lorsque le verre Sécurit (ou trempé) se casse, il doit se fragmenter en petits morceaux sans arêtes vives pour minimiser les risques de blessure. Le critère clé stipule qu’un tel échantillon doit se fragmenter en au moins 40 morceaux sur une surface de 50 mm x 50 mm.